Why 3D Printed RC Planes from Planeprint, Elision, 3Dlabprint & Flighty Are Not Reliable
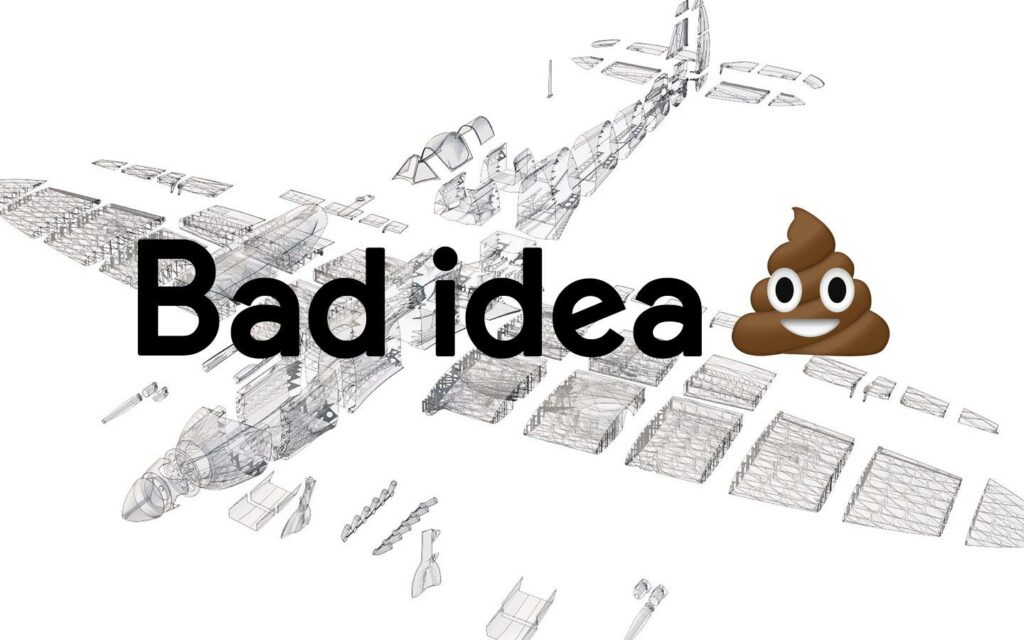
Recently, a friend of mine excitedly told me, “Hey, I just finished printing my RC plane from ***. I’m starting the build and can’t wait to fly.” Knowing the limitations of 3D-printed plastics, I was skeptical about this endeavor. A few days later, on a cool, sunny day, he took his printed plane for its maiden flight, only for it to end up in pieces after a hard landing.
You might think, “Maybe it’s a case of poor piloting or limited RC experience.” However, with over a decade of experience flying RC planes and helicopters, including competitive 3D flights and product development for RC companies, we can confidently highlight the pros and cons of 3D-printed RC planes. After testing models from brands like Planeprint, Elision, 3Dlabprint, and Flighty, here’s why we find them to be disappointing when it comes to creating durable and reliable RC planes.
1. Poor Durability in Real-World Conditions
Planeprint, Elision, 3Dlabprint, and Flighty use FDM (fused deposition modeling) to print RC planes, primarily with PLA or PETG plastics. These materials are inherently unsuited to the stress and environmental changes faced by RC planes. PLA and PETG become brittle in cold weather, making them prone to shattering, while sunlight exposure on warm days can soften and deform them. RC planes need to endure variable temperatures and resist minor impacts, something these materials simply cannot handle.
2. Lengthy Printing and Assembly Processes
While these companies offer STL files for at-home printing, the process can be excruciatingly slow. Depending on the model, printing the entire plane can take several days to weeks. Any mistakes mean reprints and further delays. Assembly is also challenging, as the printed parts are prone to breaking during gluing or other assembly steps. Unlike traditional kits, where you can make quick repairs at the field, 3D-printed planes often need a full rebuild, making them impractical for spontaneous flying.
3. Flawed Structural Integrity and Excessive Rigidity
The nature of 3D printing introduces weak points within the layers, making models vulnerable to delamination, where layers separate under stress. This issue is particularly severe in high-stress parts like wings and fuselage. Planeprint, Elision, 3Dlabprint, and Flighty’s models are also overly rigid, which increases brittleness. Without the flexibility needed for absorbing landing impacts or minor collisions, these planes crack easily, especially when landing on harder surfaces. For durability and flexibility, traditional materials like balsa wood and composites remain superior.
4. Weight and Performance Limitations
The weight-to-strength ratio of plastic is another significant disadvantage. Most 3D-printed planes end up heavier than traditional RC kits, affecting performance. Heavier planes need higher speeds to maintain stable flight, which also raises the stalling speed, making landings more challenging and low-speed turns risky. Attempting to reduce weight by using less material further reduces the plane’s structural integrity, leading to frequent breakage.
5. Limited Engine Compatibility
Unlike traditional RC planes, which can support nitro or gas engines, these 3D-printed models are limited to electric motors. The high vibration and heat of nitro engines would quickly damage 3D-printed parts. Even with electric motors, the added weight and inherent rigidity make maintaining stability difficult, leading to an unpredictable and often disappointing flight experience.
6. Structural Integrity Issues
Combining these factors results in planes with questionable structural integrity. Although plastic is frequently used in RC components, it’s rare to find fully plastic-built RC planes in commercial kits—and for good reason. The RC industry continues to rely on balsa wood, composites, and other resilient materials for their flexibility, lightness, and durability—qualities that FDM 3D-printed plastics simply cannot match.
Why Planeprint, Elision, 3Dlabprint, and Flighty Are Useless for Practical RC Flying
While brands like Planeprint, Elision, 3Dlabprint, and Flighty offer budget-friendly designs and unique customization options, their models fall short of delivering a reliable RC flying experience. Here’s why these brands aren’t ready for practical RC use:
- Excessive fragility due to the brittle nature of PLA and PETG, leading to frequent breakages on landings and impacts.
- High weight that impacts stability, raises stalling speeds, and makes low-speed maneuvers difficult.
- Assembly challenges, as gluing 3D-printed parts increases weak points and leads to cracking under stress.
- Poor weather resistance, with plastic planes degrading or breaking in variable temperatures and sunlight.
In short, Planeprint, Elision, 3Dlabprint, and Flighty are more suited for display models or experimental builds. They simply don’t provide the strength, flexibility, or weight optimization needed for RC planes that see regular use.
Are There Any Advantages?
1. Lower Cost
3D-printed RC planes are cheaper than traditional kits if you only consider the cost of the files and materials. However, electricity, printer maintenance, and additional accessories often reduce this cost advantage. Traditional ARF (Almost Ready to Fly) kits, which include most necessary components, remain an easier and more practical choice.
2. Customization and Novelty
One potential upside to 3D-printed models is the freedom to create custom or unconventional designs that may not be available from mainstream RC kit suppliers. If you’re looking for an unusual design, or just want to try something unique, these brands may have a slight appeal. However, don’t expect their designs to perform well in a range of weather conditions or under rigorous flying.
Are There Viable Alternatives?
Absolutely! 3D printing is an incredible advancement in prototyping and producing small RC parts. While it’s not suitable for full model construction, it works well for low-stress parts such as cockpit details, mold masters, and other accessories. FDM printing can also be useful for parts without direct flight stresses, like non-structural accessories.
While some brands attempt to construct entire RC planes from 3D-printed materials, innovators like Marko Roolaid and ALModel have taken a more strategic approach, using 3D printing only where it makes sense. Marko Roolaid, known for his advanced RC design insights, leverages 3D printing for specific, low-stress parts—such as cockpit details, control horns, and non-structural accessories—that benefit from the customization 3D printing allows without compromising durability. ALModels adopts a similar technique, incorporating 3D-printed elements only where they enhance functionality without adding significant weight or reducing the plane’s structural integrity. By reserving 3D printing for specialized components, Roolaid and ALModel showcase how this technology can complement traditional materials, creating RC planes that are both lightweight and reliable.
The Bottom Line: 3D Printing Has Limits in RC Aviation
For experienced RC flyers looking for performance, durability, and reliability, Planeprint, Elision, 3Dlabprint, and Flighty miss the mark. Until 3D printing materials and methods improve significantly, we recommend using traditional RC kits or hybrid approaches that integrate 3D-printed parts selectively rather than attempting a full build. At the end of the day, these brands fall short for performance-driven RC flying, making them better suited for enthusiasts interested in display models or experimental projects.